◆プリント配線板用が急増
☆紙基材フェノール樹脂積層板は、1925年より取り扱う代表的な絶縁材料ですが、1965年(昭和40年)頃になると、それまでの変圧器や発電機といった重電機用の絶縁材料としてだけではなく、新しい用途が生まれてきました。
洗濯機、冷蔵庫、扇風機、トランジスタラジオ、カラーテレビなどの家庭電化製品が普及し始めたのです。そこにはプリント配線板が多量に使われました。プリント配線板とは、絶縁板の表面に、薄い銅箔で形成された回路を持つ板のことをいいます。それまでのように部品どうしを電線でつなぐのではなく、絶縁板上の回路に部品の足を差し込んで、いっぺんにはんだ付けをおこないます。プリント配線は、機器を薄く小型化でき、作業も自動化がしやすく大量生産にも適したので、飛躍的に進歩しました。半導体は頭脳、配線板は家電の神経といわれました。
◆膨大な需要に応えるために
このプリント配線板の材料になったのが銅張り積層板です。フェノール樹脂積層板をつくる時に35ミクロンメートル(0.035mm)という薄い銅箔を重ねて同時プレスしたものでした。われわれの持っている積層板の設備がそのまま使えたのです。
ただし、その量は、重電機用の絶縁材料と比べると桁違いの大きさでした。日本の家電は技術的にも高く評価され、日本の代表的な産業となりました。その一翼を担ったプリント配線板材料への需要は膨大です。本格的に市場に参入するには、この需要に対応する設備の増強を考えざるを得ない状況にありました。
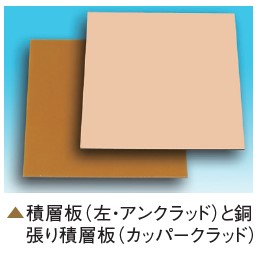
◆熱板、オープニング、プリプレグ
銅張り積層板の最終工程は、紙にフェノール樹脂を含浸した基材(プリプレグ)を何枚か重ね、一番上に銅箔をのせて加熱・加圧します。重電機用積層板のプレスは8段から10段、大きなものでも15段が最高でした。段というのは熱板と熱板の間のオープニング(開口部)で、この段の中にプリプレグを入れます。
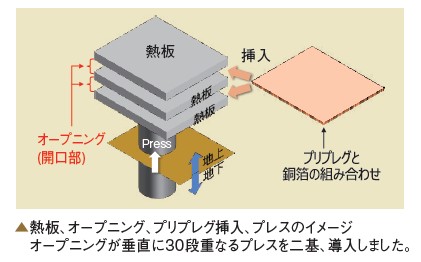
積層板の仕上がり厚さに応じた枚数のプリプレグを挿入するのですが、1mmとか2mmといった薄い板なら、1段に10枚分を仕込むことができます。8段プレスですと一度のプレスでできる積層板は80枚というわけです。熱板の大きさは1メートル四方が一般的ですから、積層板の定尺サイズは1メートル角になります。
◆業界最大となる30段のオープニング
プリント配線板用の銅張り積層板は1.6mm厚さが標準でしたが、これを効率的に大量につくるには、プリプレグと銅箔との「組み合わせ」。これをオープニングに挿入。加熱・加圧プレス。付帯作業。これらに要する時間を勘案したところ、30段がよいという結論が出ました。
30段プレスですと、1度のプレスで300枚の銅張積層板ができます。しかしそうなると、プレス機は、地上部分の高さが8メートル、地下部分が4メートル、重量は110トンにもなります。世界的にも実績がなく、その後の20年間ほどは国内最大でした。
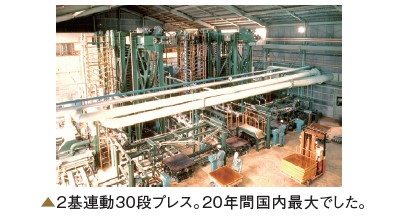
私はこの投資(約3億円)を1969年に決断し、翌年の9月に完成しました。しかも30段プレスを1基ではなく、2基発注しました。これらをプログラムコントロールで2基連動させ、プレス作業員を3分の1に減らしました。
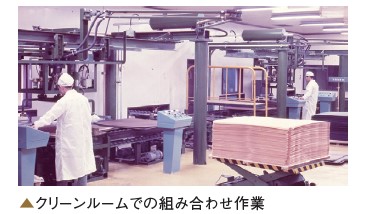
◆23メートルの地下まで
このプレスについて、私が特に考慮したことは基礎工事でした。30段プレスは1基の重さが110トン、2基で220トンになります。日本のような地震の多発国では、地震でプレスが倒れないまでも、少しでも傾くとプレスとしての機能は果たせません。調査の結果、23メートルまで掘り下げると、強固で厚い岩盤があることがわかりました。そこで23メートルまで杭を打ち込ませました。この基礎工事のおかげで、阪神・淡路大震災の時も、プレスはピリッとも傾くことなく、50年を経過した今日でも、立派に活躍してくれております。
◆起こればどうなる?
当時から私は、起こるか、起こらないか…という可能性を云々することではなく、起こればどうなる?というのが考え方の中心にありました。もし起これば大変なことになる、という場合はより慎重に物事を進めさせます。
◆ターニングポイント
白物家電に続き、ラジオ、テレビ、ステレオなど日本の電子家電が世界中に普及する時代を迎えました。それに使うプリント配線板材料である銅張り積層板の需要は急速に増大しました。
この業界初となる大型プレスの導入は、利昌工業を、中小企業から中堅企業に飛躍させるターニングポイントとなりました。
|